4 mins to read
CESAR .
Publicado em: 24 de março de 2023
CESAR and Ball: predictive maintenance and efficiency in the industry
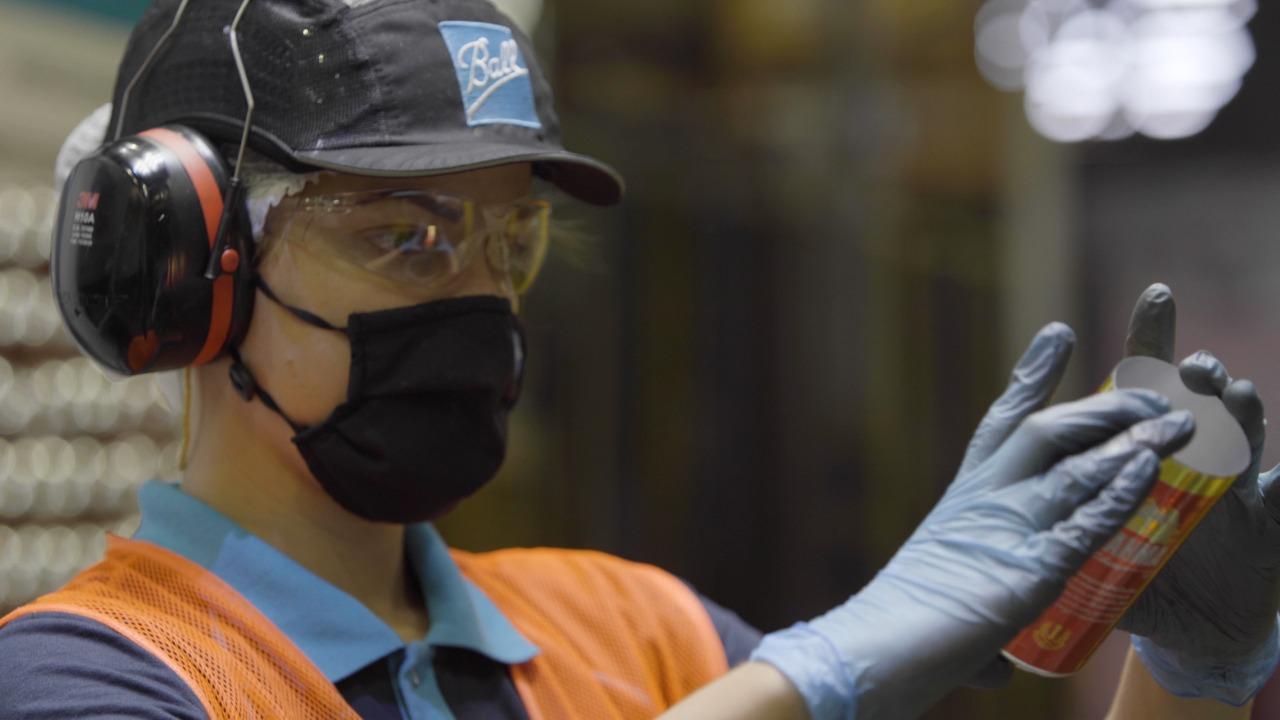
Founded in 1880 and headquartered in the state of Colorado, USA, Ball is the world’s leading manufacturer of sustainable aluminum packaging and currently has 15 industrial plants in South America. In one such plant, the local teams saw opportunities for improvement in machinery failure prevention and maintenance planning.
The company’s production was impacted by the temporary stoppage of machinery, which can lead to losses for the company. The need to reduce these losses then motivated the company to seek a partnership with CESAR.
This is how teams from the company, alongside CESAR researchers and CESAR School students, forged a path of open innovation on the factory floor in Cabo de Santo Agostinho, Pernambuco. The result is a predictive analytics solution based on data produced by sensors on the machines.
Industry 4.0: an efficiency approach on the factory production line
The predictive maintenance dashboards developed for Ball are an aid and decision-making tool for the maintenance team.The system generates a history of the machinery’s behavior and, based on this data, produces warnings if the machine starts to operate out of the ordinary, indicating the percentage of probability of a failure. Thus, the technology operates in two fields:
- Maintenance and operation: concentrates the failure predictions and even identies out-of-standard sensors and sounds alarms.
- Operational: identies which equipment is far from reaching the given targets and indicates at which speeds it needs to operate in order to reach these targets.
The solution incorporates the concept of Industry 4.0 with the use of IoT (open KNoT platform, created by CESAR) and digital technologies for data management, and has the potential to increase the company’s productivity, efficiency, and profitability. Every industry has the capability to collect data, but it is essential to determine well-targeted analysis that promotes improvements in corporate processes.
How the data was transformed into predictive analytics
In the first six months, the CESAR teams immersed themselves in Ball’s universe to understand their pain points. Which machines were used? What types of losses were faced? What relevant information could the collected data provide to improve productivity in that plant? Overall, these questions indicated more than 90,000 variables to be investigated.
After an initial analysis, it was possible to detect bottlenecks related to the machinery in the production line – for example, the equipment that tended to cause the most damage to the
process was identified. From there, analyses, metrics, and statistics were generated that served as parameters for the team’s work.
After this base was built, the work routine has revolved around storing the data generated by
the machines, saving it in the cloud, and creating dashboards to monitor the data, forecasting critical situations and guiding maintenance.
Results replicated worldwide
The results are expected to reach Ball’s plants in December 2021, with the implementation of the tool at the Cabo de Santo Agostinho plant. At this point, the project should also reach an important milestone: the transition from version 1.0 to 2.0.
“What we do today in Recife will be our calling card. By arriving at version 2.0 by the end of this year, we will prove the value of this project, collect and evaluate all the results, and be able to say whether it worked and in what predicted scenario. The next big step is to start 2022 thinking about the next plant”, reflects Bruno Giublin, Ball’s Lean Manufacturing – Industry 4.0 leader in Brazil.
Thus, the CESAR and Ball teams are working towards delivering a Minimum Viable Product of a project with great potential and that tends to grow. Since the can production process is essentially the same, the project can be replicated in Ball’s other plants in Latin America, with the possibility of expanding to other international markets.
“At the end of the day, the project provides concrete results for Ball. It improves the life of the plant; it improves the life of the person who operates the equipment; it improves the data coming into the administrative office and its operation. With the mirroring of all this in the percentage results of the plant, the whole company will understand, in practice, how far we have come. The 2022 business case will reflect all this,” says Bruno.
The partnership between CESAR and Ball was supported by the State Innovation Law,
a program to boost technological innovation created in 2013 by the Government of Pernambuco, and also by co-financing with non-reimbursable resources from the Brazilian Company of Research and Industrial Innovation (Embrapii).
Did you enjoy this case? Scale your business quickly with world-class research, design, and innovation on-demand. Get in touch